Low Pressure Permanent Mold Machines
ATD’s low pressure permanent mold machines are widely recognized for their durability, precision, and adaptability across a broad range of aluminum casting applications. As an authorized distributor, Carpenter Brothers provides technical insight and support for foundries looking to improve process control, reduce downtime, and ensure consistent casting quality.
Whether you’re producing structural components, aluminum wheels, or suspension parts, ATD equipment is designed to support efficient, repeatable performance in demanding environments.
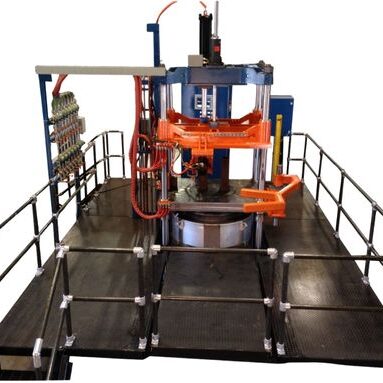
A Closer Look at the GEN III Low Pressure Casting Series
ATD’s GEN III machines are built around a proportional air control fill system, which enables smooth and stable metal flow during filling. This system helps reduce turbulence, improving overall casting integrity and minimizing inclusions or air entrapment. Combined with Allen-Bradley controls and intuitive PLC logic, these machines are built for consistency and ease of use on the shop floor.
For facilities that prioritize data tracking and process analytics, optional real-time data collection capabilities are available.
Integrated Features That Support Foundry Efficiency
Metal Gate & Wonder Slide Transfer System
A key advantage of ATD’s design is the ability to transfer molten metal between the holding furnace and pressure furnace during the casting cycle. This feature minimizes downtime and maintains a stable metal level, contributing to better casting uniformity and process reliability. No crucible changeover is required, allowing continuous operation.
Cooling Control & Flow Management
With support for up to 136 cooling lines and integration of digital flow meters, ATD machines offer detailed thermal management. Flow meters can be programmed by time or temperature and embedded directly into part recipes — allowing foundries to tailor cooling to specific casting geometries and alloys.
Safety Considerations
ATD casting equipment incorporates several operator safety features, including a SITEMA safety catcher and die safety blocks. These components provide mechanical fail-safes during mold handling, helping foundries meet workplace safety standards without adding complexity to the workflow.
Cope Tilt for Mold Access
On larger models, a Cope Tilt Mechanism allows the upper half of the mold to tilt beyond 90 degrees, making it easier to inspect and maintain the mold surface. This can help reduce downtime related to touch-ups or coating issues, particularly in higher-volume operations.
Applications
ATD low pressure permanent mold machines are commonly used in:
-
Automotive aluminum wheel production
-
Structural component casting (e.g., crossmembers, knuckles)
-
Suspension parts and chassis elements
-
Custom aluminum parts requiring precise, repeatable quality
Available features for low-pressure permanent mold machines include:
-
Wide range of sizes
-
Digital flow meters are available
-
Proportional air control fill system
- Cope tilt mechanism on larger GEN3 machines
Supporting Your Casting Operation
At Carpenter Brothers, our role is to provide practical guidance and connect metal casters with the right equipment for their production goals. If you’re exploring options for upgrading your casting systems or need support selecting the right configuration, we’re here to help.
Whether you’re evaluating automation needs, planning a facility upgrade, or simply gathering information, we’re available to answer questions and share technical resources.
Learn More or Start a Conversation
If you’d like to learn more about ATD’s low pressure casting equipment or discuss potential applications in your operation, feel free to reach out.