Foundry Products Metal Casting Products
Carpenter Brothers, Inc. offers a complete line of foundry products and equipment to meet the requirements of the Metal Casting Industry.
Carpenter Brothers, Inc. offers a full line of metal casting consumable products. Products that are used in the ferrous, non ferrous, investment casting and die casting industries.
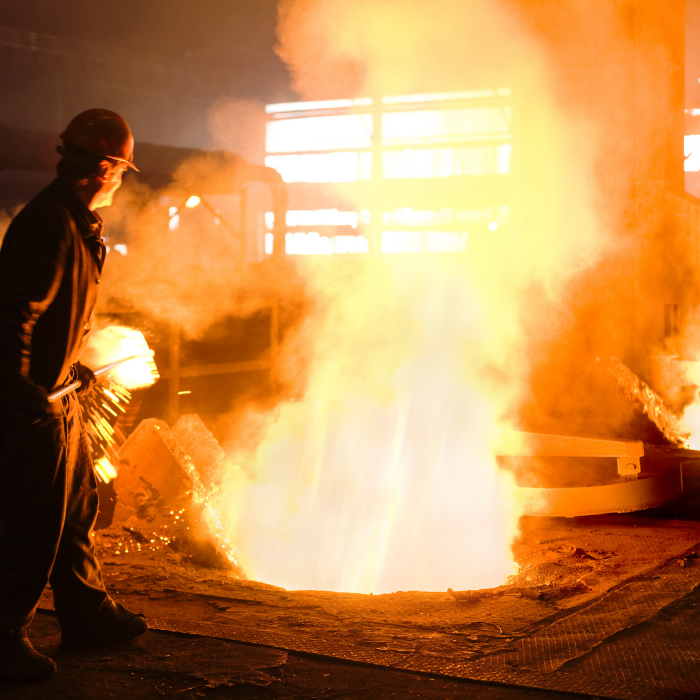
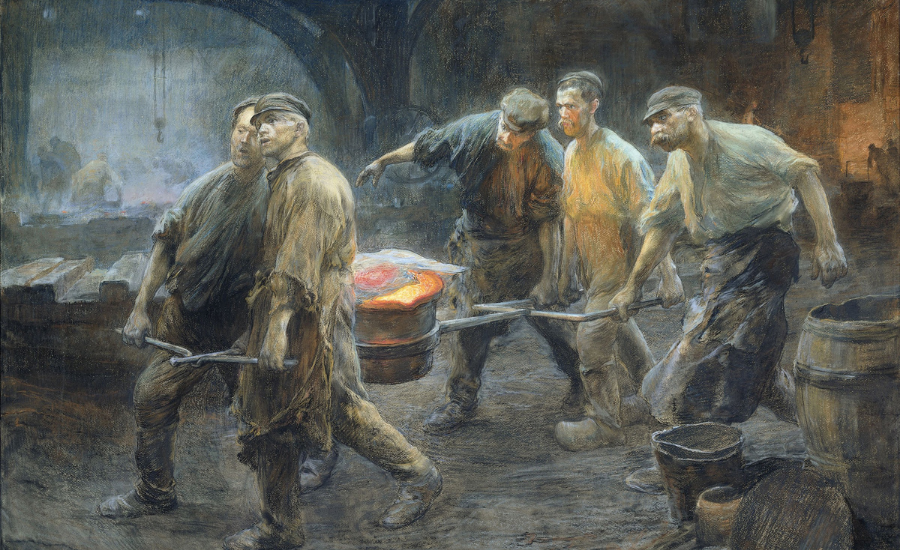
Foundry Products
We offer products and solutions for every department in your foundry.
Die Casting Products
We offer various products for melting, measuring, and moving aluminum.
Foundry Products
We supply the necessary foundry products you need to make a quality casting. Whether you need Metals & Alloys, Melting & Melt Quality, Molding & Core Making, Casting & Shakeout, Finishing & Surface Preparation, or Environmental Compliance products we have what you need.